Combining Sludge Drying and Thermal Hydrolysis: How to Optimize Energy Consumption and Improve Drying Efficiency
Discover how combining sludge drying with thermal hydrolysis can optimize energy consumption and improve efficiency in wastewater management. Learn about the benefits, challenges, and best practices for integrating these two powerful sludge treatment processes.
9/12/20244 min read
Introduction
Sludge management is one of the biggest challenges in wastewater treatment. With increasing urbanization and industrial activities, the volume of sludge generated has skyrocketed, making efficient disposal a critical concern. Traditional methods are not only resource-intensive but also often environmentally unsustainable. This is where combining sludge drying with thermal hydrolysis comes into play—a powerful approach that optimizes energy consumption and enhances drying efficiency.
By integrating these two processes, wastewater treatment facilities can achieve more efficient sludge management, lower operational costs, and significantly reduce their environmental footprint. But how exactly does this combination work? Let’s dive deeper into the world of sludge drying and thermal hydrolysis to explore the benefits of their synergy.
Understanding Sludge Drying
Before we get into the benefits of combining sludge drying with thermal hydrolysis, let's start with the basics. Sludge drying is the process of reducing the moisture content of sludge to make it easier to handle, transport, and dispose of.
Benefits of Sludge Drying in Wastewater Management
Sludge drying offers several advantages:
Volume Reduction: Removing water content reduces the volume of sludge, making transportation and storage easier.
Cost Savings: Dried sludge is cheaper to transport and dispose of, saving money in the long run.
Resource Recovery: In some cases, dried sludge can be repurposed as a soil conditioner or even as a source of energy.
Common Methods of Sludge Drying
Several methods exist for sludge drying, including belt dryers, drum dryers, and solar drying. Each method has its own set of pros and cons, depending on the specific needs and constraints of the facility.
Introduction to Thermal Hydrolysis
Now, let’s shift focus to thermal hydrolysis, a process that uses high temperature and pressure to break down complex organic matter in sludge.
How Thermal Hydrolysis Works
Thermal hydrolysis involves heating sludge to temperatures of around 150–170°C under pressure. This "cooks" the sludge, breaking down cell walls and converting complex organic compounds into simpler, more easily digestible forms for microbes during subsequent digestion processes.
Benefits of Thermal Hydrolysis in Sludge Treatment
Improved Biogas Production: Makes sludge more amenable to anaerobic digestion, enhancing biogas production.
Reduced Sludge Volume: Lowers the volume of sludge, reducing disposal costs.
Pathogen Reduction: Achieves pathogen destruction, making the sludge safer for reuse.
The Synergy of Sludge Drying and Thermal Hydrolysis
Combining sludge drying with thermal hydrolysis brings out the best in both processes. But why should these two be combined?
Why Combine Sludge Drying with Thermal Hydrolysis?
When these processes are used together, they enhance each other’s effectiveness. Thermal hydrolysis reduces the moisture content and makes the sludge less viscous, while sludge drying removes any remaining water, producing a dry, easy-to-handle product.
Key Benefits of the Combination for Wastewater Management
Energy Efficiency: Less energy is needed for drying since thermal hydrolysis pre-treats the sludge.
Enhanced Drying Efficiency: Reduced sludge volume and improved sludge characteristics make drying quicker and less costly.
Improved Sludge Quality: Higher-quality end products, such as pathogen-free biosolids, can be achieved.
Optimizing Energy Consumption Through Thermal Hydrolysis
One of the key advantages of thermal hydrolysis is its potential to significantly reduce energy consumption in sludge drying. Here’s how:
How Thermal Hydrolysis Reduces Sludge Volume and Moisture Content
Thermal hydrolysis breaks down the organic matter, releasing bound water and making the sludge less bulky. This pre-treatment step means that less energy is needed during the subsequent drying process.
The Impact of Reduced Moisture on Drying Energy Requirements
Lower moisture content means that the sludge requires less heat energy to reach the desired dryness level. This translates to substantial energy savings, especially when applied to large volumes of sludge.
Enhancing Drying Efficiency with Thermal Hydrolysis
Not only does thermal hydrolysis optimize energy use, but it also enhances overall drying efficiency.
Improving Sludge Characteristics for Easier Drying
By breaking down complex molecules, thermal hydrolysis changes the physical properties of the sludge, making it less sticky and more uniform. This allows for faster and more even drying.
Faster Drying Times and Reduced Operational Costs
With less water to remove and better sludge consistency, drying times are shortened, and the equipment works more efficiently. This leads to lower operational costs and reduced wear and tear on machinery.
Technical Considerations for Integration
To successfully integrate sludge drying with thermal hydrolysis, certain technical considerations must be addressed.
Required Equipment and Infrastructure
Facilities need to have or invest in equipment that supports both processes, such as reactors for thermal hydrolysis and appropriate dryers.
Key Factors to Consider for Effective Integration
Factors such as sludge composition, volume, and specific facility requirements should be carefully evaluated to determine the best approach for integration.
Maintenance and Operational Considerations
Regular maintenance of equipment and training for staff are critical to ensure smooth operation and maximum efficiency.
Environmental and Economic Benefits
Combining these two processes offers numerous environmental and economic advantages.
Lower Greenhouse Gas Emissions
The integrated approach leads to lower energy consumption, reducing greenhouse gas emissions.
Reduced Disposal Costs
With less volume and moisture, disposal becomes easier and less costly, further contributing to sustainability.
Potential for Resource Recovery (e.g., Biogas Production)
Thermal hydrolysis enhances biogas production during digestion, creating an additional revenue stream for facilities.
Potential Challenges and Solutions
While there are many benefits, integrating these processes also presents challenges.
Technical and Operational Challenges
Some facilities may face challenges related to equipment compatibility or operational expertise.
Mitigation Strategies and Best Practices
Proper planning, equipment selection, and staff training can help mitigate these challenges.
Future Advancements to Watch
Ongoing research and technological advancements are expected to further optimize these combined processes.
Conclusion
Combining sludge drying with thermal hydrolysis is a game-changer for wastewater treatment facilities looking to optimize energy consumption and enhance drying efficiency. With the right approach, this powerful combination can lead to significant cost savings, reduced environmental impact, and improved overall sludge management.
FAQs
What are the initial costs of combining sludge drying with thermal hydrolysis? Initial costs can vary widely depending on the size of the facility, equipment needed, and existing infrastructure. However, long-term savings in energy and disposal costs can offset these investments.
How much energy savings can be expected? Energy savings will depend on the specific processes and equipment used, but reductions of up to 50% in drying energy requirements have been reported in some cases.
Are there specific types of sludge that benefit more from this combined approach? Yes, sludge with higher organic content typically benefits more from thermal hydrolysis, which makes the subsequent drying process more efficient.
What is the lifespan of equipment used in this process? With proper maintenance, equipment for both thermal hydrolysis and sludge drying can have a lifespan of 10-20 years.
Can smaller facilities also implement this combination effectively? While the initial investment may be significant, smaller facilities can also benefit from this combined approach, especially if they face high sludge disposal costs or have opportunities for biogas production.
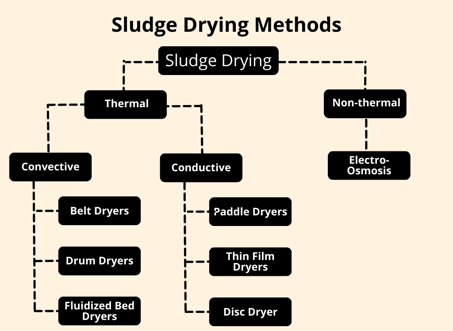
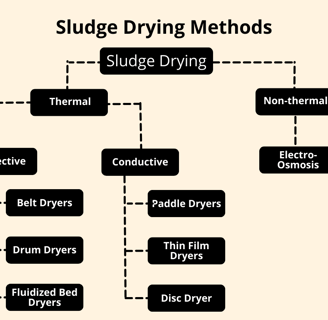
JXX is a family-run business established in 1998, dedicated to providing customers with the most suitable drying equipment to make their production work more efficient, smooth, and environmentally friendly.
Products
Contact
+86-137-7501-3369
© 2024. All rights reserved.